Oil Analysis "Cost vs Price"
- Dean Hempel
- May 11, 2023
- 2 min read
Oil analysis is normally something for big contractors and commercial consumers of lubricants. The lab testing of both new and used oils makes perfect sense when you consider the ever increasing cost of equipment purchases. Developing an oil analysis program for each piece of equipment can reduce the overall costs.

One of the most commonly watched is 'wearing metals' because it can indicate some warning signs of a major failure. While it doesn't guarantee a breakdown can't happen, it can prevent an unexpected failure. Let's face it, a breakdown is never convenient. The chart above shows a typical track in wear metals vs miles for a vehicle. You can see that the normal wear metals are shown in a slight increase slope. Normal wear expects to see an increase in metals as the miles increase. However, you can see from the chart when there was an increased PPM of wear metals indicating "Abnormal" wear taking place. Catching this before an unexpected failure is a huge advantage.
Wear metals appear in oil under 'normal' wear conditions. The oil analysis program helps determine extending drain intervals based on real data. Costs per mile/hour is determined by oil, filters, labor, and of course breakdowns. If an oil analysis program can help reduce costs and extend the life of equipment, it can make a big difference in the bottom line.
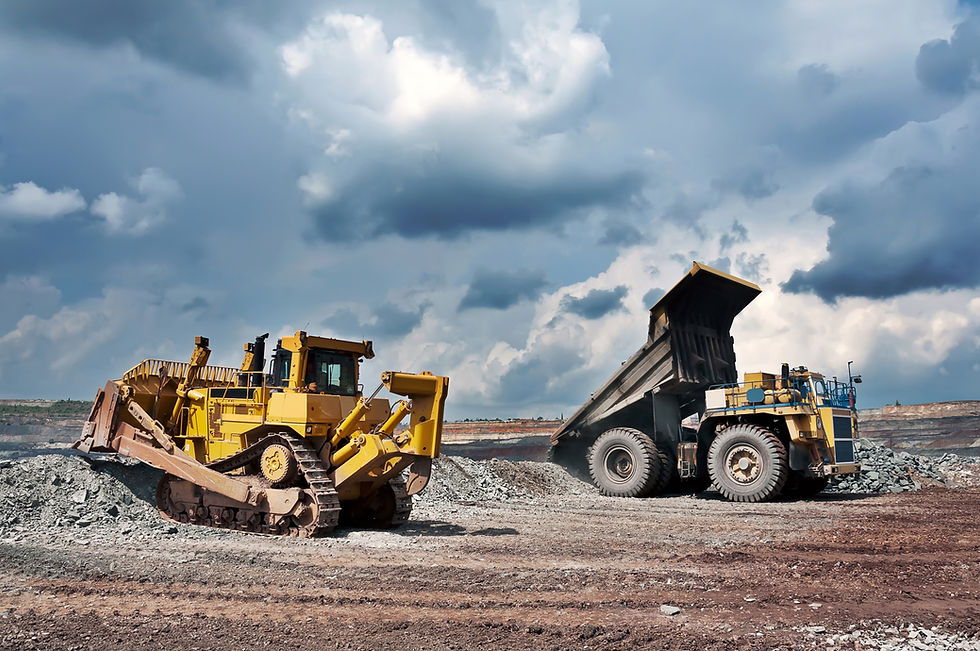
The oil analysis provides a comparison with extreme accuracy, down to PPM (Parts Per Million). Then there are those micro contaminants that are too small to be filtered out. Normally they are not a concern unless the total amount is excessive to a point of causing operational failure. Oil analysis also looks and many other contents within the oil sample that can be helpful without ever turning a bolt on the engine. Oil analysis is not the answer for every fleet or commercial application, but it does need to be considered for a cost saving. The cost for the analysis must be part of the overall calculation taking into account the equipment, oil, filter, labor and breakdown (downtime). If equipment breaks down on the job its cost is much much higher than repairing in a pro-active situation.
At Direct Performance, we utilize a team of experts to determine if an oil analysis program will be cost effective for your situation. Also, we do our best to cover the most important areas to your specific needs. When we complete a cost comparison, it reveals that lower prices can result in higher costs. Even without a crystal ball to see the future precisely there are tools that can help your commercial equipment do the job for you.
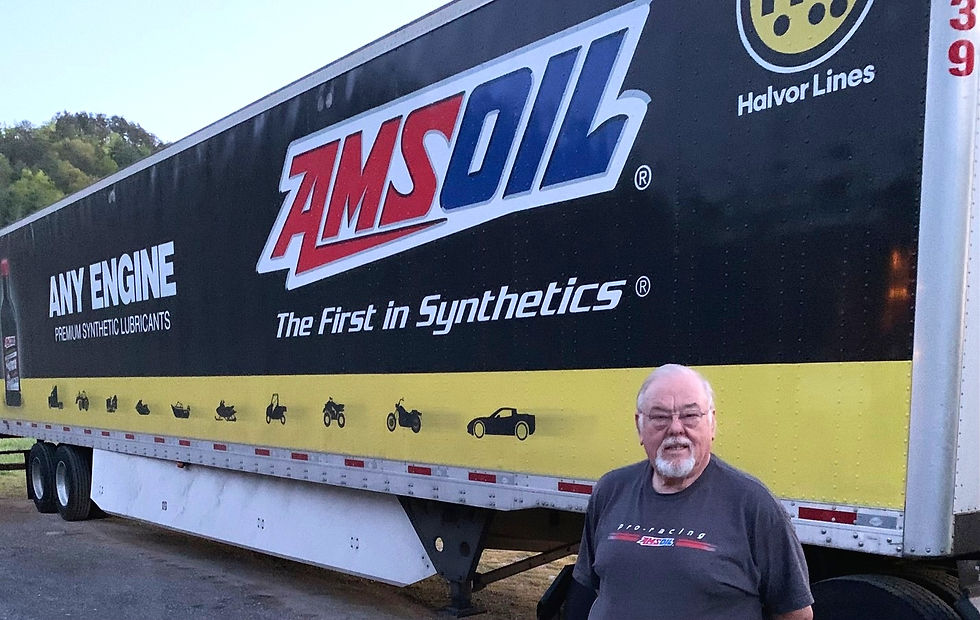
Comments